Some metal optics makers focus just on the plating and polishing operations, which may be a workable strategy for simple optics. Complex metal optics, however, have specifications that are difficult or impossible to meet without a vertically integrated manufacturing operation.
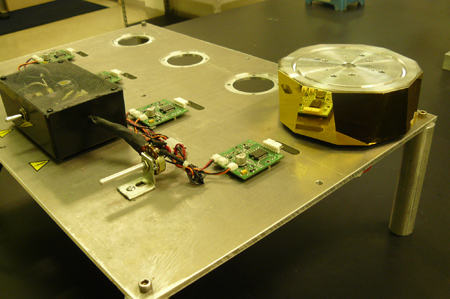
True vertical integration means that a single supplier performs all the crucial processes of metal optics production, including:
- Machining
- Plating
- Polishing
- Diamond turning
- Coating Assembly
- Testing, metrology and environmental validation
Each of these manufacturing steps has the potential to introduce optical or mechanical defects. And when these optical manufacturing steps are carried out by different suppliers, the defects can be difficult, time consuming and costly to find and fix for two simple reasons:
- Logistical risk. Moving parts back and forth between multiple suppliers adds time and cost to the production process. And all the additional handling during transit increases risk of damaged parts.
- Requirement misinterpretation. Even when governed by stringent specifications, different suppliers can have slightly different interpretations of the long list of requirements that typically define a complex optical component. Many of these requirements, by their nature, can be somewhat subjective. This problem of interpretation has practical implications in the form of inconsistent workmanship and poor optical performance.
SEAMLESS MANUFACTURING SYSTEM
By combining all the optical manufacturing steps into a seamless system, vertically integrated optics suppliers avoid the problems caused by a fragmented supply chain. This integrated approach minimizes threats of supply chain disruption, while optimizing cost, quality, and manufacturing cycle time.
Keep in mind that integrated assembly matters every bit as much as the optical production steps. Sloppy assembly practices can leave even the best-made metal optic susceptible to distortion from CTE mismatches or other sources of mechanical stress.
Testing, too, shouldn't be overlooked as a valuable part of an integrated optics manufacturing operation. Aside from saving time and money compared to contract testing, in-house in-process testing provides the immediate feedback needed to fine-tune sequential optical manufacturing steps.
To take one example of the value of a vertically integrated manufacturing approach, we produce optical polygon motor assemblies and balance them in-house. Feedback from the balancing operation has led to improvements to the uniformity of material removed by diamond turning. The improved uniformity, in turn, simplifies the balancing process.
Had the assembly and balancing process taken place downstream of our integrated operation, our customers would not have been in a position to provide the ongoing feedback that led to our diamond turning process improvements. And our customers may have assumed the need for complex balancing procedures was inherent in the optical manufacturing processes.
RISK MITIGATION
Vertical integration does more than ensure that all optical and mechanical requirements are satisfied and validated. Vertically integrated optics suppliers remove risk from the supply chain–by eliminating the possibility of non-performing subcontractors.
The technical and supply chain advantages of vertical integration carry much weight with the military, but civilian metal optics users can benefit too. Vertical integration makes sense whenever metal optics need to be at their best.